Drilling spot welds and swapping panels (more)
Moderator: FORDification
- 67nukeford
- Blue Oval Fan
- Posts: 589
- Joined: Tue Aug 19, 2008 3:20 pm
- Location: Nebraska, Omaha/Elkhorn
Re: Drilling spot welds and swapping panels
I'm considering doing this to the cab that I picked up. I may take a borescope from here at work and put it down into the cowl, to see how much rust is there, and to see if it would be needed.
-
- New Member
- Posts: 19
- Joined: Thu Aug 12, 2010 1:26 am
Re: Drilling spot welds and swapping panels
how do you get the windshield out?
-
- 100% FORDified!
- Posts: 22329
- Joined: Sun Aug 28, 2005 8:17 pm
- Location: Kansas, Ottawa
- Contact:
Re: Drilling spot welds and swapping panels
cut the rubber around the windshield. then buy a new rubber to reinstall the windshield.
- flyboy71
- Blue Oval Guru
- Posts: 1012
- Joined: Sat Mar 21, 2009 9:30 pm
- Location: Boiling Springs, PA
Re: Drilling spot welds and swapping panels (more)
Im moving onto replacing some panels on a decent rust free cab. The dash is all dented and dinged and the rear panel inside the cab was cut and patched with a crappy welded chunk of steel so I need to replace both of them. I already pulled a dash from a donor cab and tonight I pulled the rear panel from the same cab. I had yanked the dinged dash over the weekend and the better dash fits perfectly. Now I need to pull the rear panel, pound some dents out of the cab exterior sheet metal and then weld the donor rear panel in. I took some pics of it all so everyone can see whats involved and what lurks behind it all.
Not so perfect dash pulled
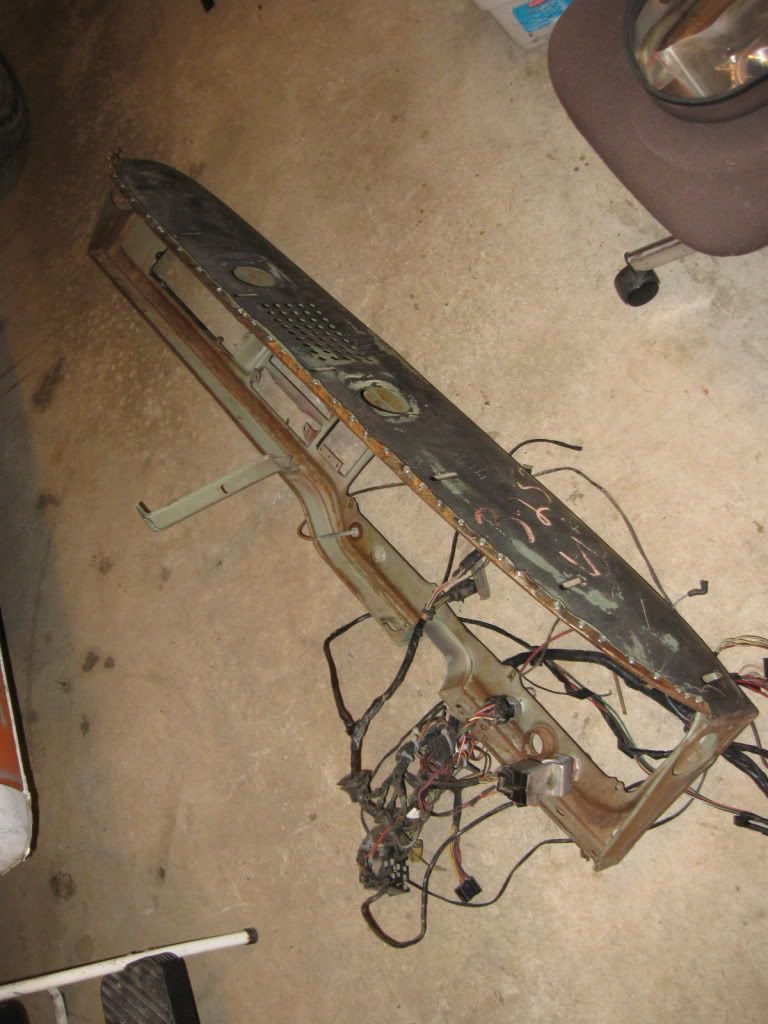
Donor dash clamped in place
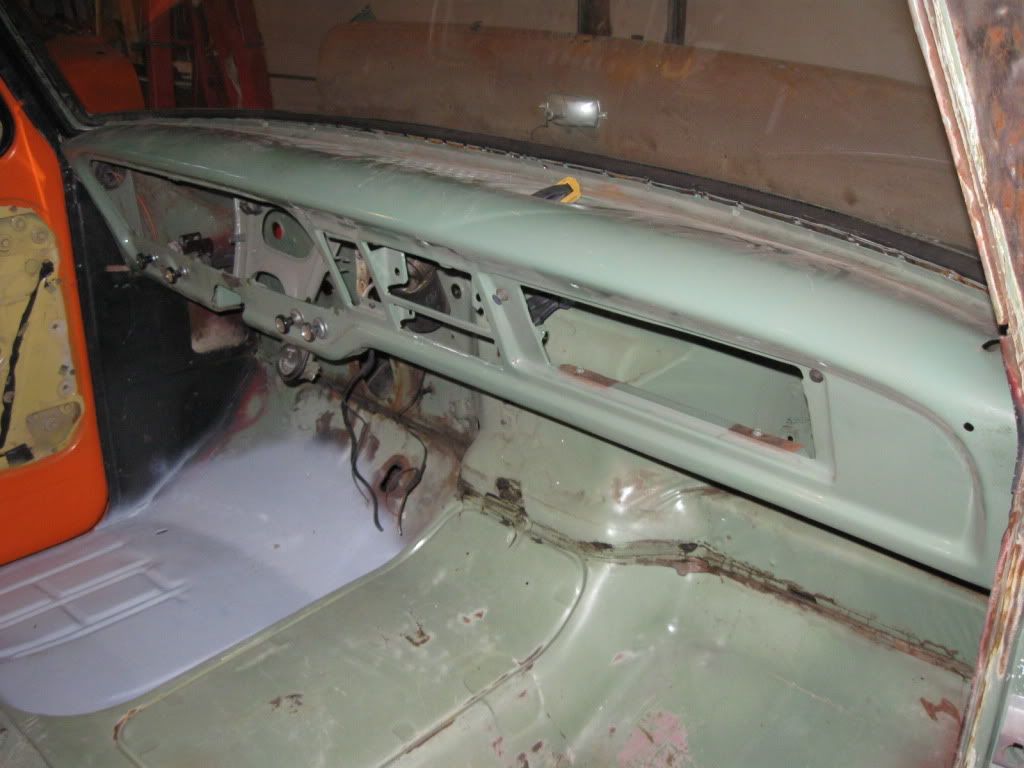
Rear cab panel pulled
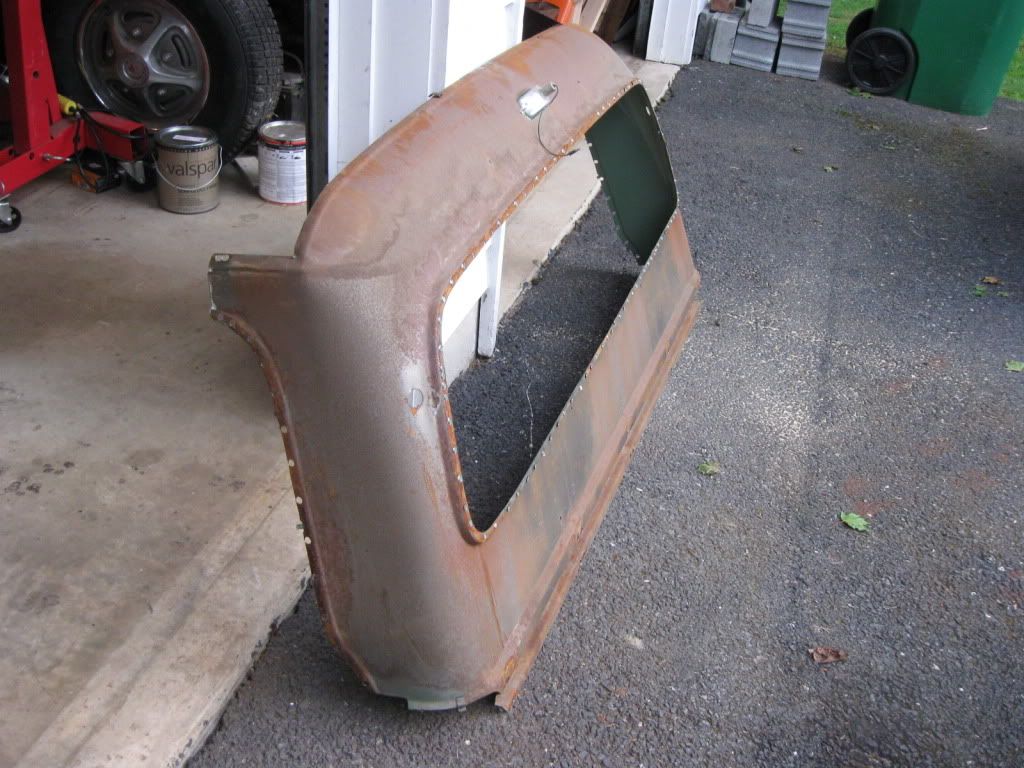
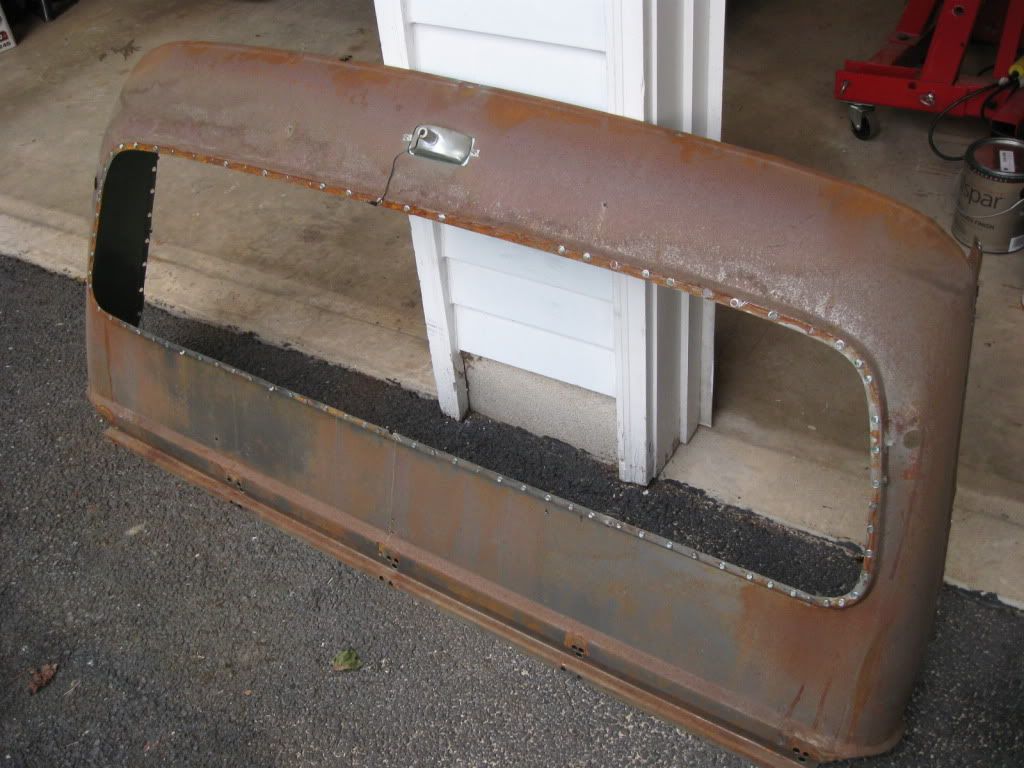
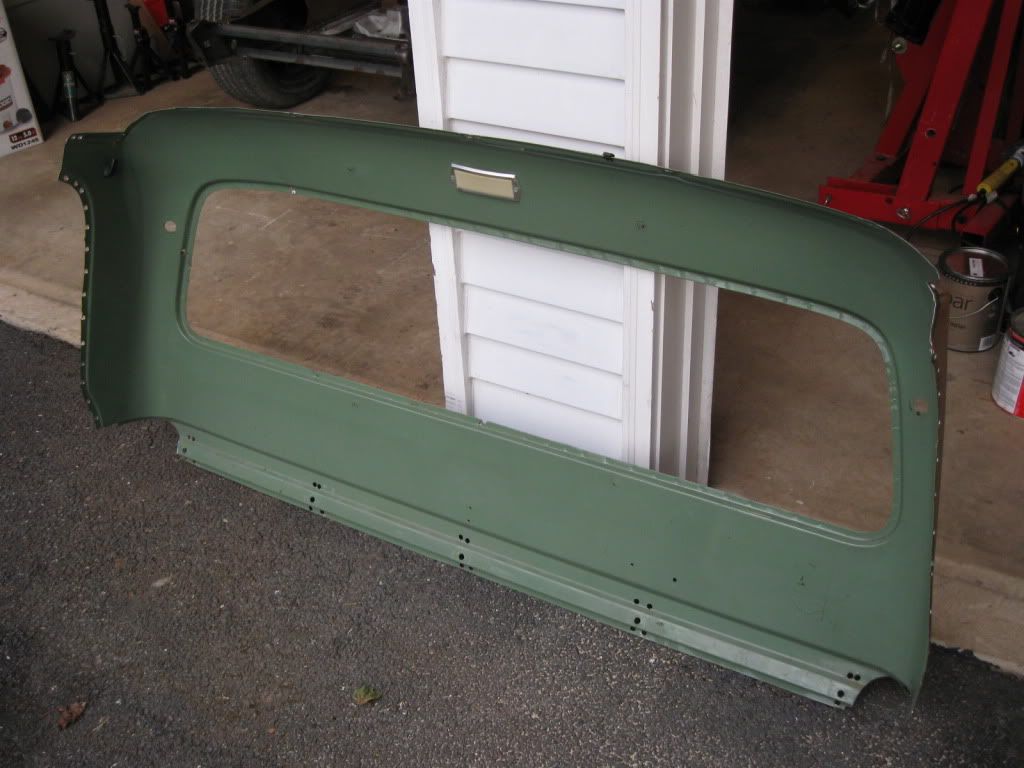
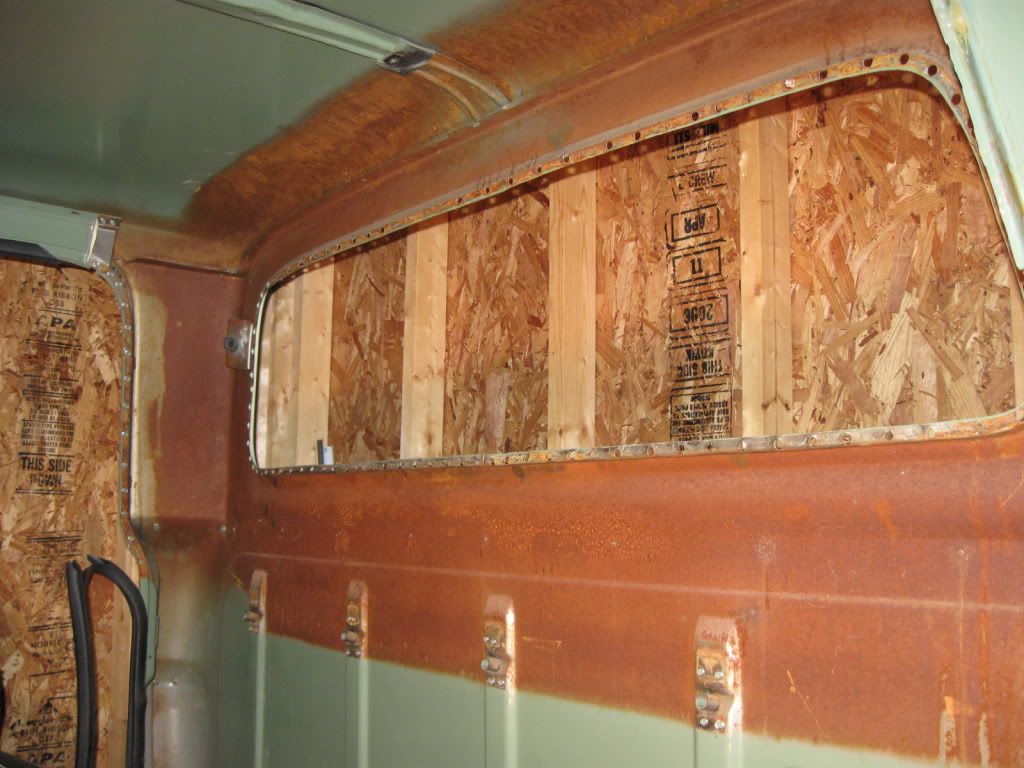

Not so perfect dash pulled
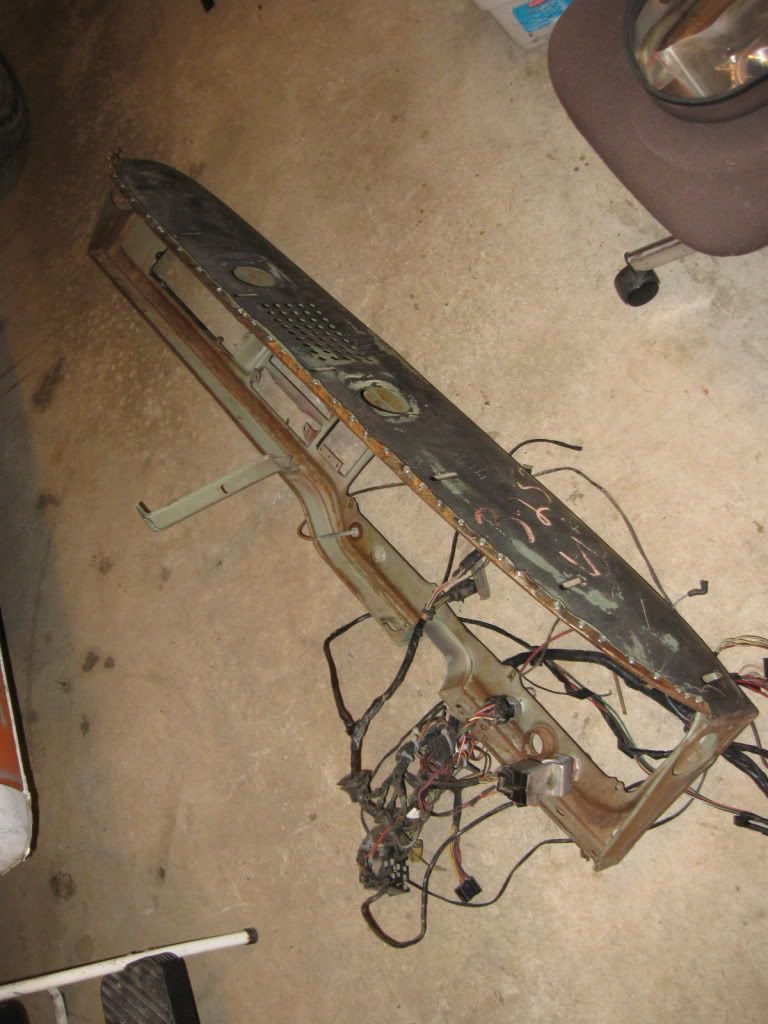
Donor dash clamped in place
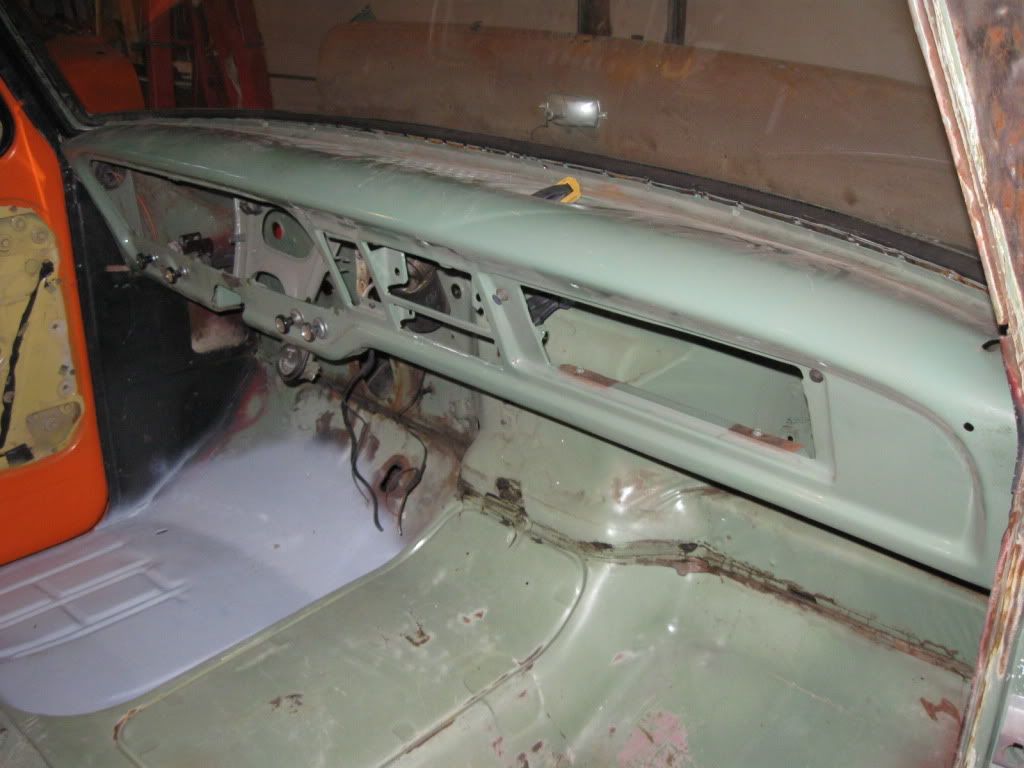
Rear cab panel pulled
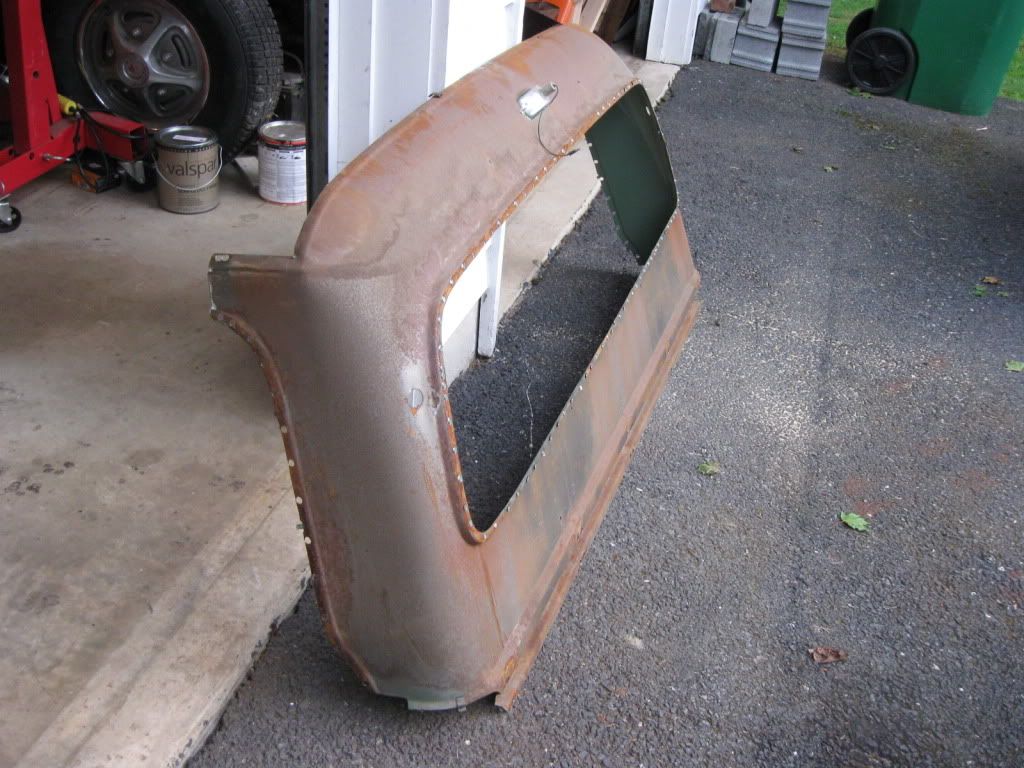
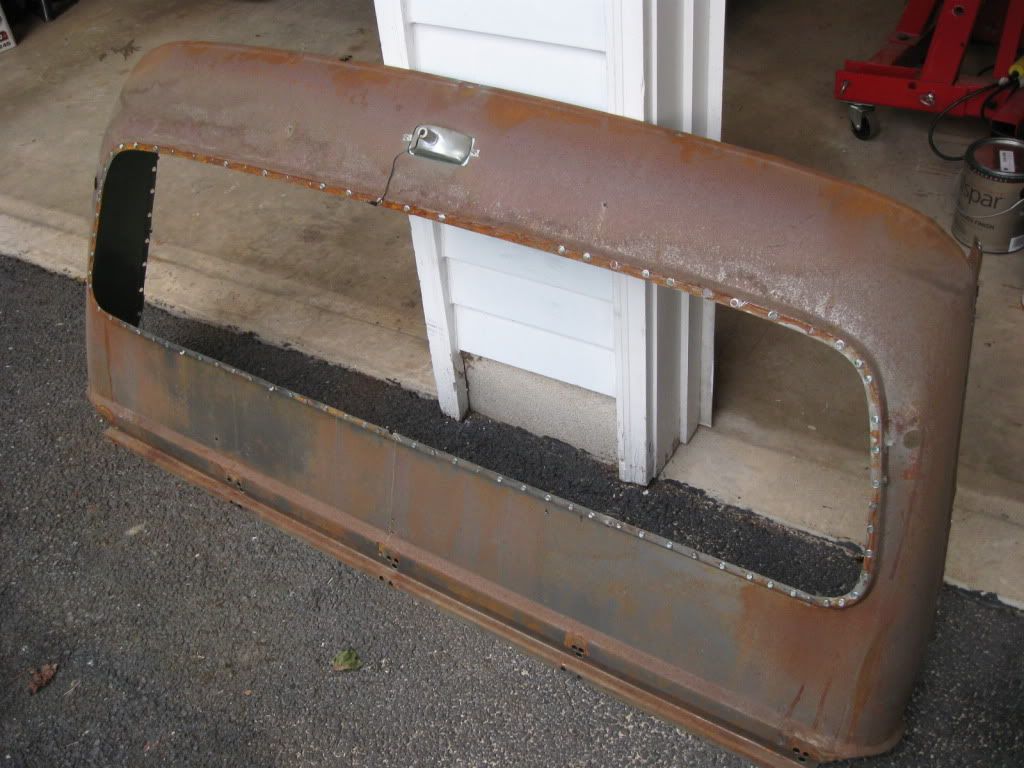
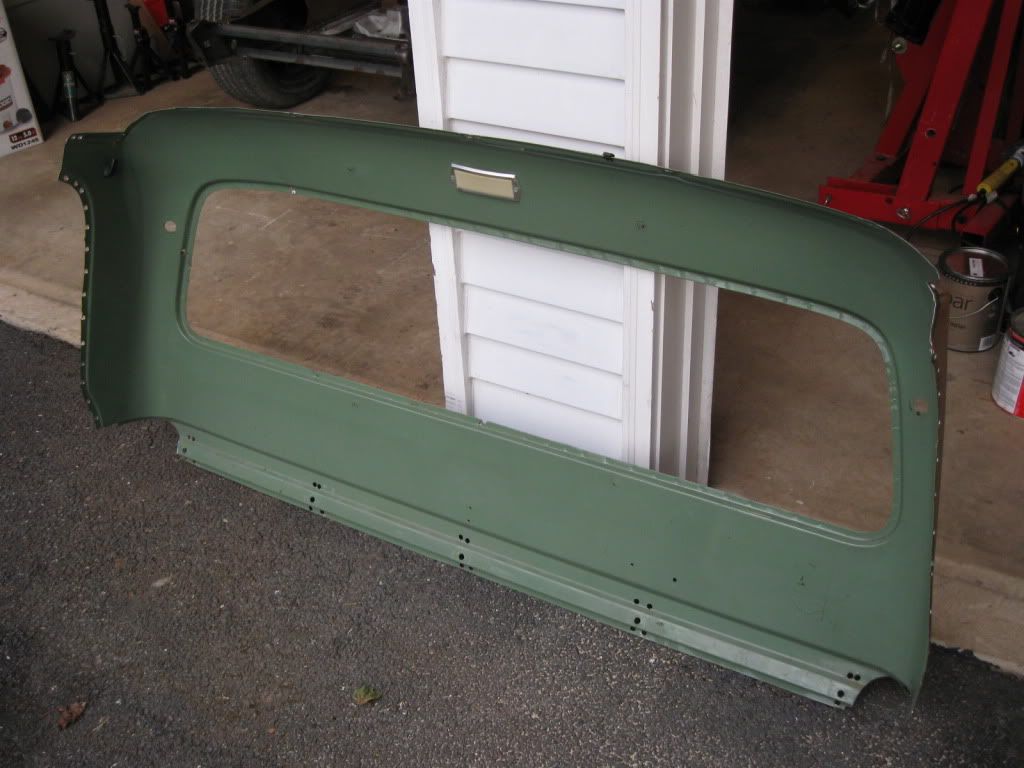
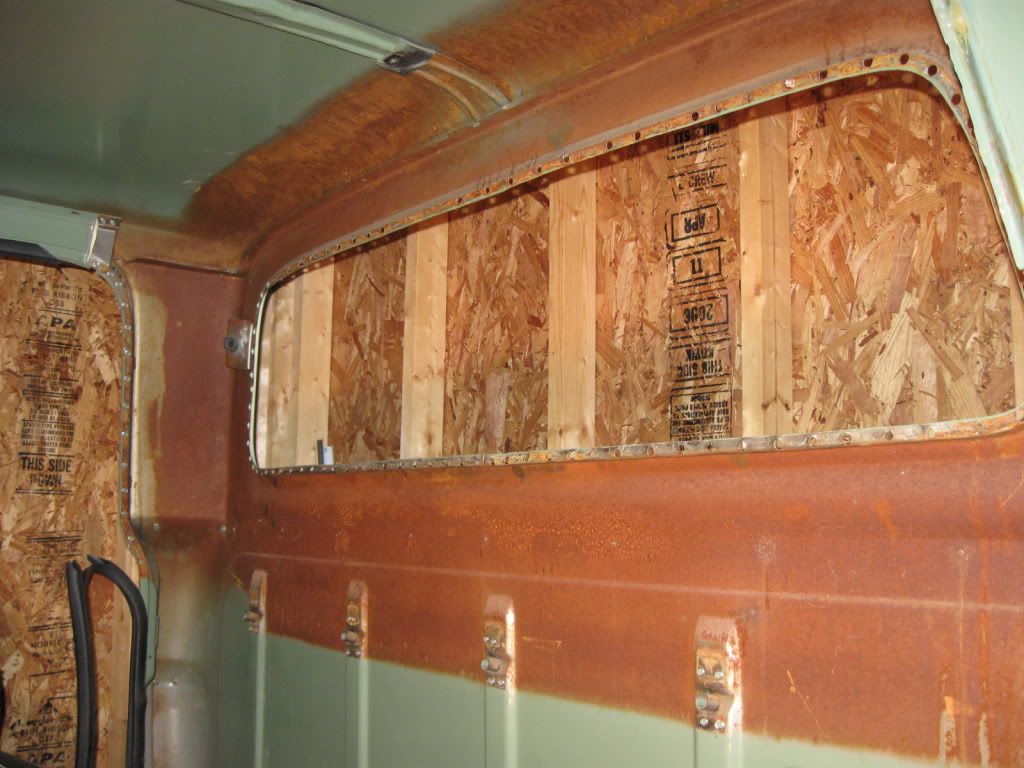
-Jeff
1971 F-100 240 straight six, 3 on the tree (parted out)
1972 F-100 302 auto trans, pwr steering, pwr brakes (under construction)
"Things are more like they are now than they ever were before" Dwight Eisenhower
1971 F-100 240 straight six, 3 on the tree (parted out)
1972 F-100 302 auto trans, pwr steering, pwr brakes (under construction)
"Things are more like they are now than they ever were before" Dwight Eisenhower
-
- 100% FORDified!
- Posts: 22329
- Joined: Sun Aug 28, 2005 8:17 pm
- Location: Kansas, Ottawa
- Contact:
Re: Drilling spot welds and swapping panels (more)
that is cool . i like it. being able to get it apart like that. with not having to cut sections off or out. we need to have this thread held soemplace so it can always be found as reference material.
- flyboy71
- Blue Oval Guru
- Posts: 1012
- Joined: Sat Mar 21, 2009 9:30 pm
- Location: Boiling Springs, PA
Re: Drilling spot welds and swapping panels (more)
Ill see if I can write up something and put it on the BumpWiki
Heres why Im replacing the rear panel. I pulled the bad one tonight. It looks like a porcupine got a hold of someones welder. The inside is all ground and mangled too from poorly ground welds.
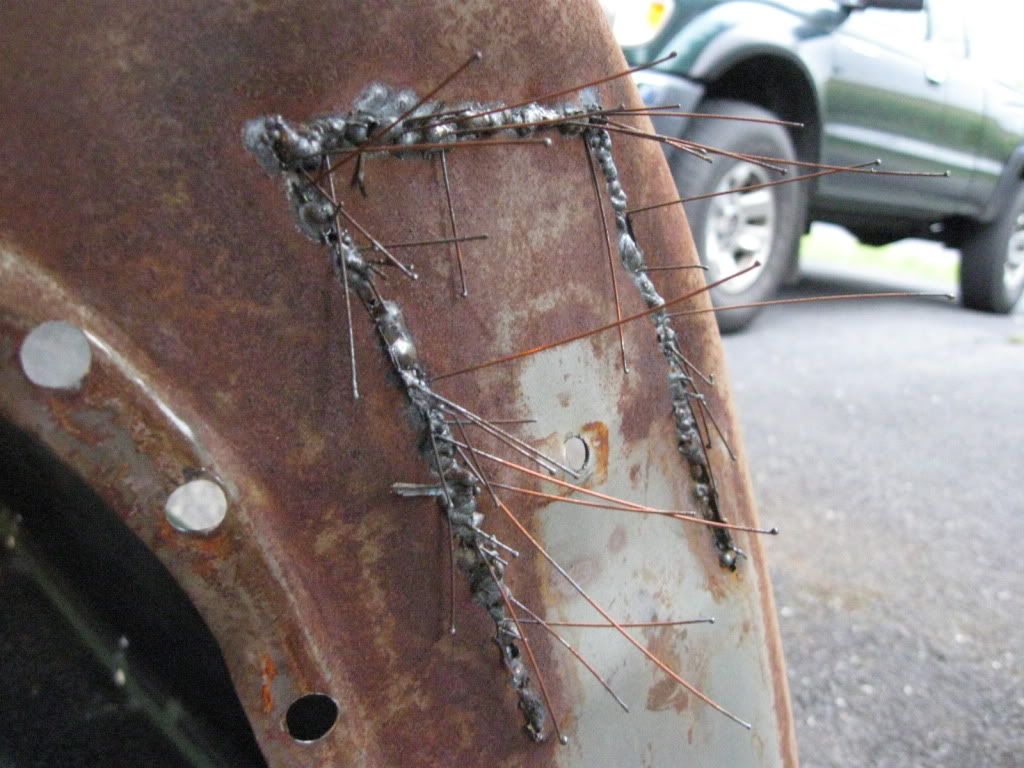
Heres why Im replacing the rear panel. I pulled the bad one tonight. It looks like a porcupine got a hold of someones welder. The inside is all ground and mangled too from poorly ground welds.
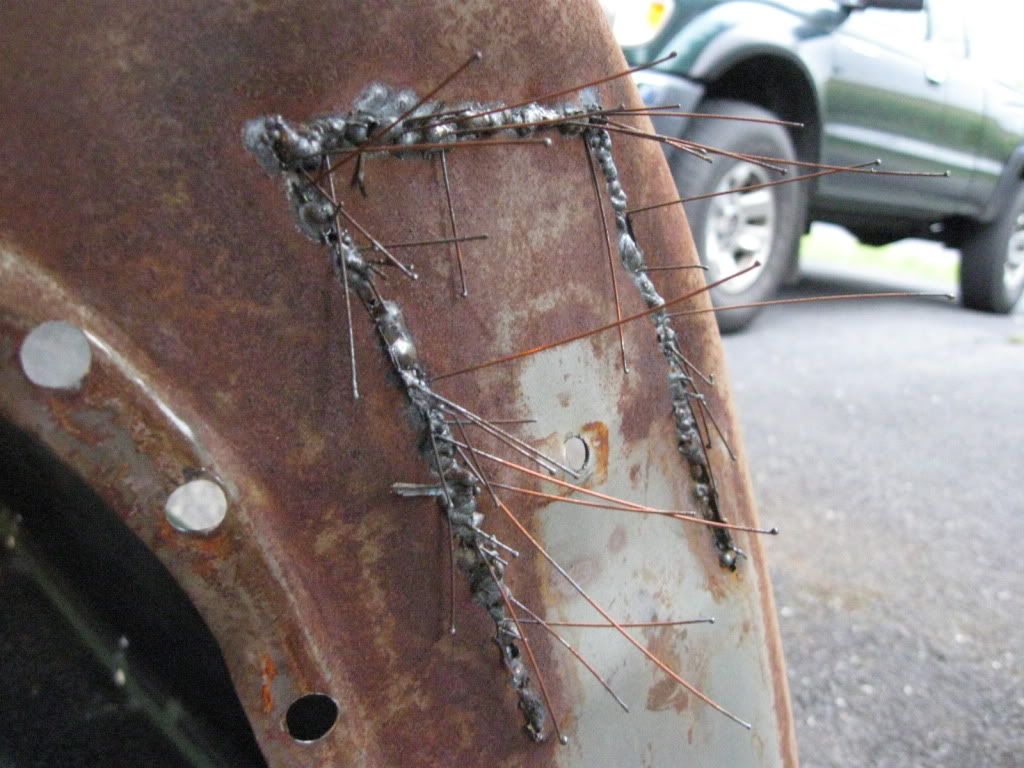
-Jeff
1971 F-100 240 straight six, 3 on the tree (parted out)
1972 F-100 302 auto trans, pwr steering, pwr brakes (under construction)
"Things are more like they are now than they ever were before" Dwight Eisenhower
1971 F-100 240 straight six, 3 on the tree (parted out)
1972 F-100 302 auto trans, pwr steering, pwr brakes (under construction)
"Things are more like they are now than they ever were before" Dwight Eisenhower
-
- 100% FORDified!
- Posts: 22329
- Joined: Sun Aug 28, 2005 8:17 pm
- Location: Kansas, Ottawa
- Contact:
Re: Drilling spot welds and swapping panels (more)
seat belt bolt hole problems i would guess.
- flyboy71
- Blue Oval Guru
- Posts: 1012
- Joined: Sat Mar 21, 2009 9:30 pm
- Location: Boiling Springs, PA
Re: Drilling spot welds and swapping panels (more)
Actually that hole in the middle is the coat hook. I think the previous owner tried to peel the metal back and pound out some wrinkled metal thats on the outside of the cab just behind the door. They did a poor job of patching it up though. At least now I can get to that wrinkle and use a hammer and dolly and fix it the right way before I weld the other panel in. 
One thing though, you can see that Ford never painted the panels judging by the surface rust and lack of any kind of paint/primer. I can paint it now before I put it back in too.

One thing though, you can see that Ford never painted the panels judging by the surface rust and lack of any kind of paint/primer. I can paint it now before I put it back in too.

-Jeff
1971 F-100 240 straight six, 3 on the tree (parted out)
1972 F-100 302 auto trans, pwr steering, pwr brakes (under construction)
"Things are more like they are now than they ever were before" Dwight Eisenhower
1971 F-100 240 straight six, 3 on the tree (parted out)
1972 F-100 302 auto trans, pwr steering, pwr brakes (under construction)
"Things are more like they are now than they ever were before" Dwight Eisenhower
-
- 100% FORDified!
- Posts: 1928
- Joined: Fri Oct 23, 2009 1:06 am
- Location: Williamsburg,Virginia
Re: Drilling spot welds and swapping panels (more)
Flyboy, I have to give you
for digging into it knee deep.
How long did it take you to pull the panel ?



- flyboy71
- Blue Oval Guru
- Posts: 1012
- Joined: Sat Mar 21, 2009 9:30 pm
- Location: Boiling Springs, PA
Re: Drilling spot welds and swapping panels (more)
It only took me a couple hours to drill and pull it. Hardest part is all the spot welds. You need a few breaks in there to give your arms a break and grab another cold one. I used a wide putty knife to get between the panels and break any remaining bond at the welds but its fairly easy if you drill them dead center. On the rear cab panel there isnt any seam sealer but on the cowl there was and that makes it a little more difficult to pry it apart with the adhesion that gives.
-Jeff
1971 F-100 240 straight six, 3 on the tree (parted out)
1972 F-100 302 auto trans, pwr steering, pwr brakes (under construction)
"Things are more like they are now than they ever were before" Dwight Eisenhower
1971 F-100 240 straight six, 3 on the tree (parted out)
1972 F-100 302 auto trans, pwr steering, pwr brakes (under construction)
"Things are more like they are now than they ever were before" Dwight Eisenhower
-
- New Member
- Posts: 19
- Joined: Thu Aug 12, 2010 1:26 am
Re: Drilling spot welds and swapping panels (more)
im trying to post some pics(phone issues).
i just got my cowl off, and the part of the firewall that connects to the dash, cause it was beyond repair.
i took a look in my spare cab's cowl and saw paint instead of rust so...more drilling those welds, started the other night, going to do more tonight.
this post has been key!! which reminds me, flyboy, how was that middle piece between the cowl and dash on your truck?
i just got my cowl off, and the part of the firewall that connects to the dash, cause it was beyond repair.
i took a look in my spare cab's cowl and saw paint instead of rust so...more drilling those welds, started the other night, going to do more tonight.
this post has been key!! which reminds me, flyboy, how was that middle piece between the cowl and dash on your truck?
- flyboy71
- Blue Oval Guru
- Posts: 1012
- Joined: Sat Mar 21, 2009 9:30 pm
- Location: Boiling Springs, PA
Re: Drilling spot welds and swapping panels (more)
Im trying to figure out how to post all this on the BumpWiki with instructions and guidelines on where the seams are. Its somewhat easy to follow them but it can get tricky around the door pillar where it wraps around at the top hinge.
The panel under the cowl is fine on both of mine. Somehow it didnt rust out. The donor is by far worse so I wont be needing it. The cab Im putting all this on is a cab from the desert SW so there is ZERO rust anywhere except surface rust. Im not used to pounding on a cab and having the only thing to fall on the floor is a pile of desert sand. I love it! Im replacing the panels that are too hard to patch or arent worth the hassle. I can weld little circles but cant put a patch panel in a gaping hole and make it look good to save myself.
If you need help just let me know.
The panel under the cowl is fine on both of mine. Somehow it didnt rust out. The donor is by far worse so I wont be needing it. The cab Im putting all this on is a cab from the desert SW so there is ZERO rust anywhere except surface rust. Im not used to pounding on a cab and having the only thing to fall on the floor is a pile of desert sand. I love it! Im replacing the panels that are too hard to patch or arent worth the hassle. I can weld little circles but cant put a patch panel in a gaping hole and make it look good to save myself.
If you need help just let me know.
-Jeff
1971 F-100 240 straight six, 3 on the tree (parted out)
1972 F-100 302 auto trans, pwr steering, pwr brakes (under construction)
"Things are more like they are now than they ever were before" Dwight Eisenhower
1971 F-100 240 straight six, 3 on the tree (parted out)
1972 F-100 302 auto trans, pwr steering, pwr brakes (under construction)
"Things are more like they are now than they ever were before" Dwight Eisenhower
- Bumpside Collector
- Preferred User
- Posts: 452
- Joined: Sun May 16, 2010 4:11 pm
- Location: Near Hot Springs, Arkansas
Re: Drilling spot welds and swapping panels (more)
Man this is a really cool thread!! I have some hoods that I was thinking about doing the same thing with. I have one hood that is flawless except for the front area where the letters are. There are several places that are totally rusted through. In total there is probably over a foot of rust holes. I have some other hoods that are beat up everywhere else but are good in the nose. I think I'll try this out on the hoods. When you go back together how do you plan on welding? Are you just going to run a bead around where you cut out the spot weld?

CHEESE?!?
Running:
2012 Ford Focus SE hatchback
2007 F-150 XLT Supercrew 4.6 Auto
1972 F-350 Flatbed 360 2V 4 speed
Not Running:
1967 F-100 Ranger Short Bed
1970 F-100 Ranger Long Bed
1972 F-100 Ranger XLT long Bed
1972 F-350 Really long dump flatbed parts truck
1981 F-250 Custom Long Bed (Parting out now)
- flyboy71
- Blue Oval Guru
- Posts: 1012
- Joined: Sat Mar 21, 2009 9:30 pm
- Location: Boiling Springs, PA
Re: Drilling spot welds and swapping panels (more)
I have hoods in the same situation but havent looked at where the spot welds are at on those yet. I plan to just plug weld the holes where I drilled out the welds. On all the panels so far the holes land on metal on the opposite panel except for maybe two places where the welds were at the same location. I may buy some plug weld pliers to weld those since it has a copper plate on one jaw that allows you to build up weld without it sticking. Im close to actually welding so Ill post pics when I do. Im still practicing on scrap right now.
-Jeff
1971 F-100 240 straight six, 3 on the tree (parted out)
1972 F-100 302 auto trans, pwr steering, pwr brakes (under construction)
"Things are more like they are now than they ever were before" Dwight Eisenhower
1971 F-100 240 straight six, 3 on the tree (parted out)
1972 F-100 302 auto trans, pwr steering, pwr brakes (under construction)
"Things are more like they are now than they ever were before" Dwight Eisenhower
-
- New Member
- Posts: 100
- Joined: Tue Aug 31, 2010 4:52 pm
Re: Drilling spot welds and swapping panels (more)
you should be able to weld hole shut that small without useing a backer start on one end and work the pool to other end and let off at just the right time mabey try twice let cool a littel and do agian worst thing is it blows thru and you can try agian. i am assuming you are mig welding. welding is a easy task to learn but takes years to master. insted of expencive pliers i use a piece of copper pipe actually i have three in my box 3/8 1/2 & 3/4 all are 3-4 in long smashed flat on one end and wraped in tape on other cause they can get hot quick! the old body men i learned from 20 years ago taught me that trick .they used copper pipe and welded alot of chrome trim and emblem holes on the old cars. on the new cars we repair for insurance companies our collision guidlines are to replace more welds than we cut out because we have changed the metal strenth buy cutting / welding / grinding / ect... (heating & cooling) make sure to use weld thru primer before welding that will make repair last longer than you .
wes

You do not have the required permissions to view the files attached to this post.
69 bronco 4x4 - 70 bronco tube chassies 4x4 351-w c-6 - 65 f-100 w/69 429- c-6 - 03 ranger 4x4 - 99 f-350 4x4 diesel