Hi all,
So the polishing went okay - I think stainless steel was a good place to start (tough and more forgiving than aluminum trim), and I started with the back window trim as per my previous post. These pieces needed very little polishing, but if you recall from the start of this thread, Smokey was in a fire which must have spread to the rear window gasket as when I removed the gasket over a year ago, it was like a charcoal brick. The stainless just had a brown haze which needed some grey Scotch Brite initially, and it polished out okay with the stand-mounted polisher (see pic above). I did have a bit of trouble with the inside curves, and probably could have used Jamie's (Ranchero's) advice regarding balling electrical tape up the retaining nut on the outside edge of the polishing wheel. Luckily, I have a spare set, so was able to polish up one nice complete set.
The front stainless was actually a bit tougher. In the prairie provinces, we have a lot of gravel roads with takes a toll on the front half of any vehicle. I watched the YouTube videos on repairing stainless, and took out dings with a variety of tools, mainly a flat b*stard file. This worked pretty good, but left pretty heavy scratches that needed +++ 80 grit sandpaper and a lot of elbow grease to smooth out. I then went to 180, 240, 300, 400, 600 grit dry, then 600 wet sand. I found this didn't get all scratches out, so I re-watched some of the YouTube Videos. I found that it is necessary to sand in the one direction at 30 degrees or so, and do the opposite to get the cross hatch pattern. I spent a lot more time working the 180 grit to get the 80 grit scratches out, and so on, probably sanding at least one hour for each piece with dent repairs, and finishing with 1000, then 1500, then 2000 grit wet sanding. After polishing with the grey stainless compound, then white and red rouge respectively, the result was pretty good, but not quite brand new looking. At that point, I decided "good enough" for a truck, as all of the pieces are still quite shiny and brilliant. Three out of the 6 pieces are literally perfect 10/10 show quality (the driver's side piece is NOS...polished up perfect

). If I would do it all over again, I would use a 120 or 140 grit either between or in place of the 180 grit after the 80 grit, as I don't think the 180 grit is quite enough to get out the 80 grit scratches by hand. Maybe a small dual-action orbital sander would work better at that point.
Some pics:
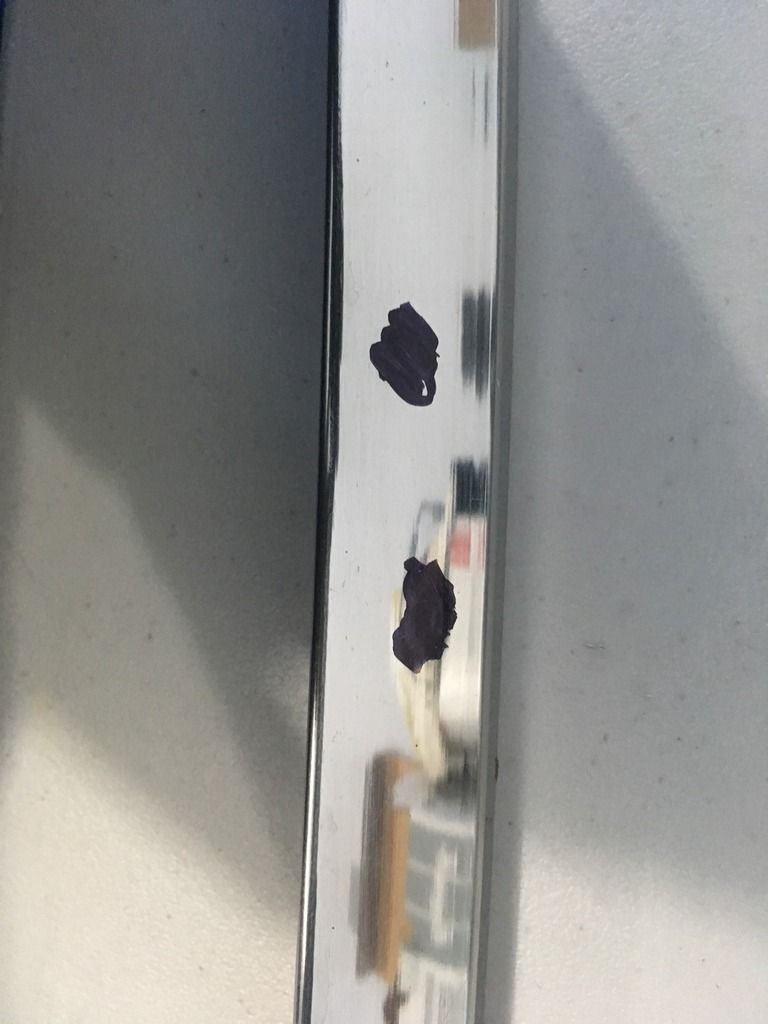
Colored in the dents with a Sharpie to help determine when to stop filing.
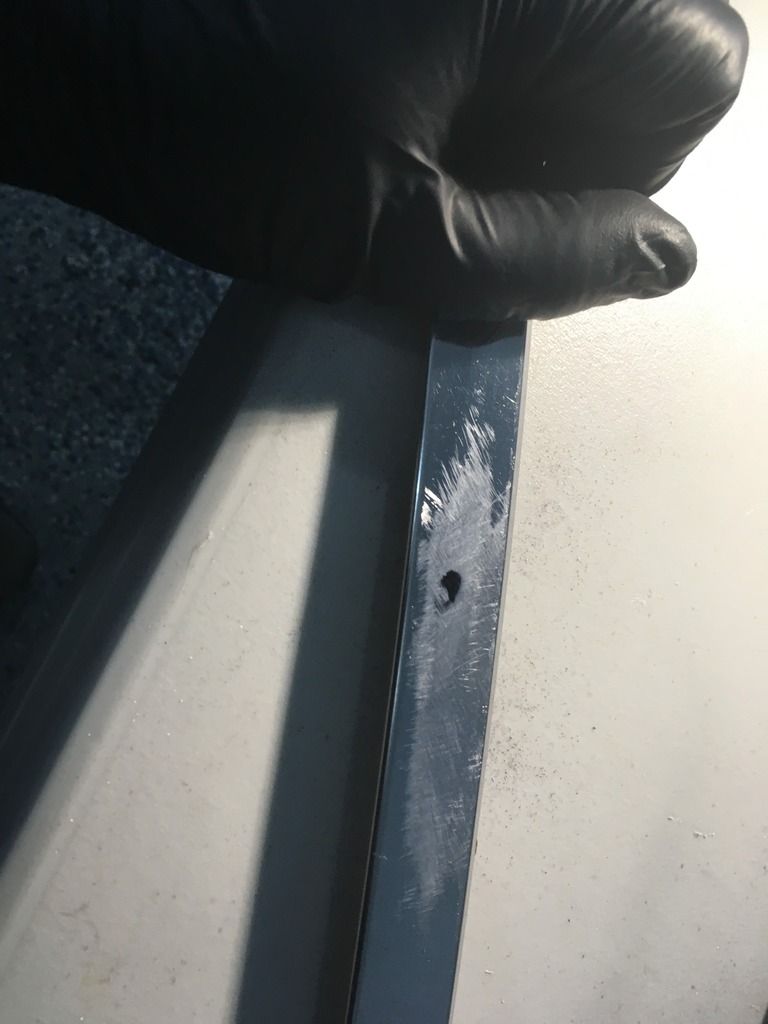
Filing away with my "flat b*stard" (seriously, that is what the packaging calls it

)
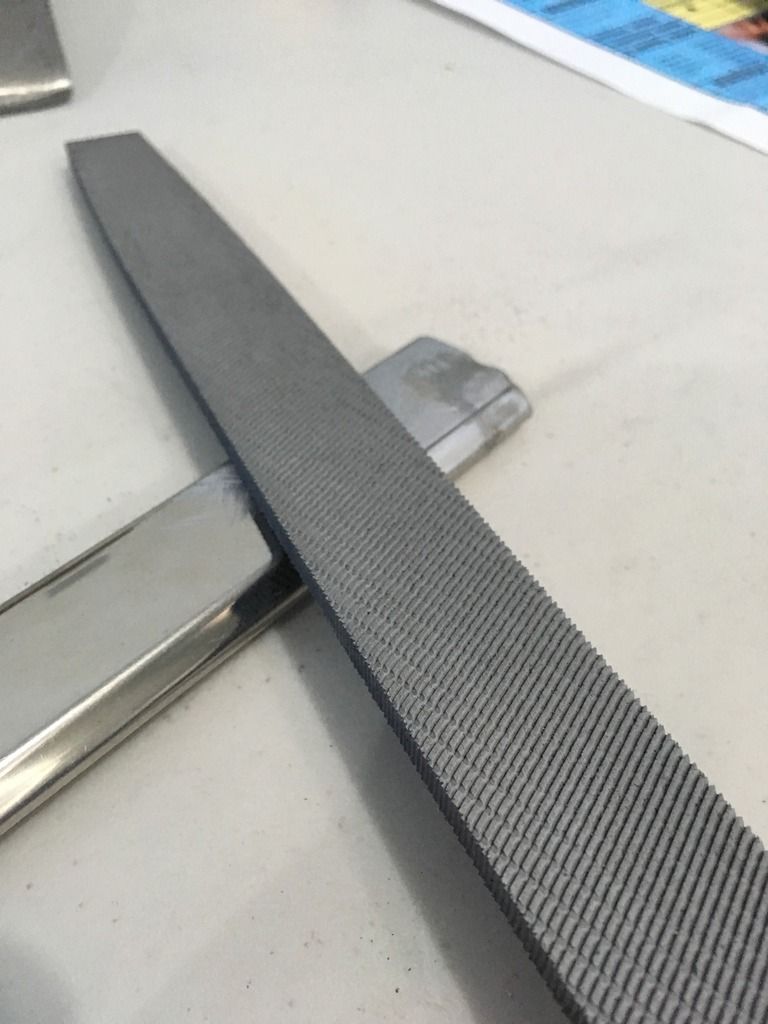
The flat b*stard file that I used - perhaps it is too aggressive as it leaves some fairly deep gouges.
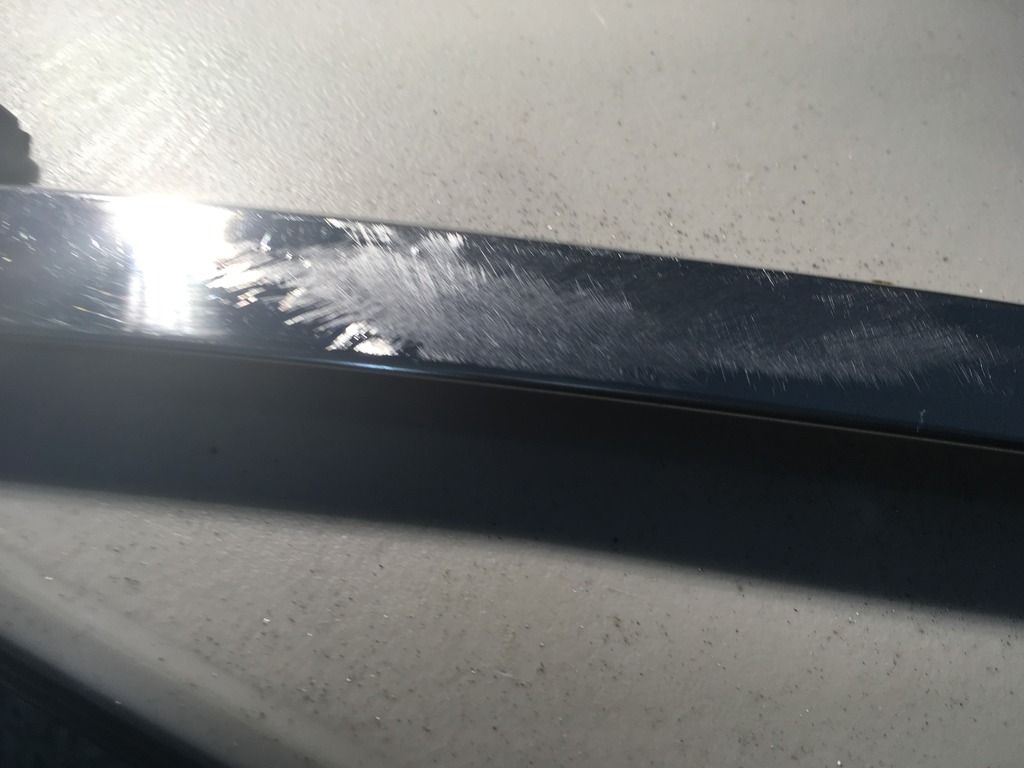
Cross hatch pattern.
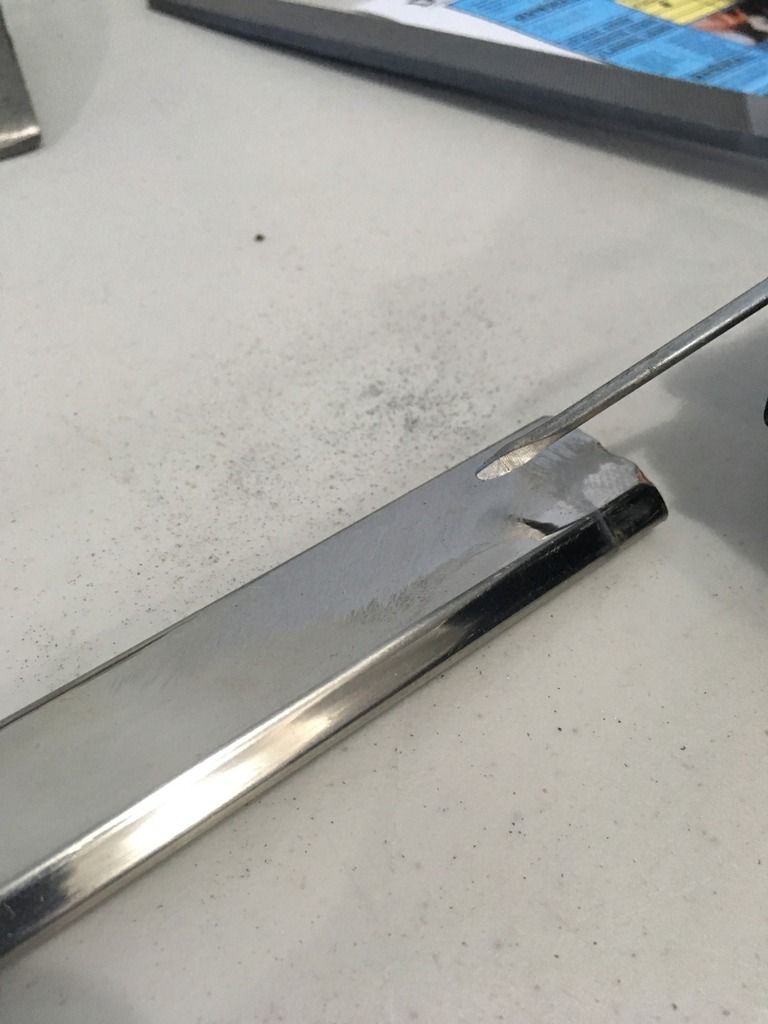
this small screwdriver that I accidentally rounded off the edges has been quite handy. I used it here to push up some dents that I had trouble getting to, as half of these pieces are 2 layers of stainless folded over. I wasn't able to get between the layers of stainless, but did find that those dents were shallow and could be filed flat without filing through the layer entirely.
I'll get out some pics of the finished front trim once they are installed by the glass company - stay tuned!
The stand-mounted polisher took some getting used to. Personal protective equipment is a must (coveralls with no loose cuffs, heavy gloves (I used the heavy latex-dipped ones that allowed me to hang on to pieces), safety googles, dust mask, and face shield), and the "booth" that I configured around my garage door tracks and hardware kept the dust limited to that area of the garage. I found it important to keep control of the piece (no more that 6 inches between my hand and the wheel), as the polisher likes to flip the piece up and hit the shaft or the retaining nut. The curvy or small pieces I used a drill and a bob with compounds, which actually worked okay. I didn't bolt it to the polisher stand to the floor, but found that three 18kg boxes of kitty litter worked very well to hold it down, and I put a layer of rubberized matting for lining tool box drawers which kept the vibrations down and protected my nice epoxy garage floor. The polisher is certainly not for the faint of heart, and deserves a lot of respect (perhaps more than most power tools).
My Western Jr. mirrors will be next on my polishing list. I plan to hit the curved pieces with the drill/bob, and straight sections with the polisher. There will be a few dings to take out on the backs of the mirrors, which should be interesting as I can't get the flat b*stard file on the large flat sections...perhaps 40 grit sandpaper, unless anyone else has a smarter idea...
I will also have to polish my aluminum grille and XLT tailgate trim piece eventually. The stainless has been good practice in working up to those pieces (I think). I plan to practice on a few aluminum pieces that are otherwise scrap. Any comments or advice on my process above, or with polishing aluminum is welcome (either plug it into this thread, or PM me).