DuckRyder, thanks for the reply. I'd like reply to this one in the forum, rather than by PM's, etc., because I think it makes a good topic for discussion, and may provide insight to other forum members.
Okay, what you said is good, and mostly supports my previous post.
Correct, the crankshaft is designed to ride on a film of oil under pressure. That is true when there is rotation of the shaft. At rest, there is no flow of oil, because it is not required. However, there is still a film of oil left on the crankshaft and the bearings that will provide lubrication when the engine is turned over and until the oil pump supplies additional lubrication.
You are correct, a load is placed directly on the bearing shell when the engine is raised by the crankshaft. The load is placed on a small surface area, as you suggest. Again,
However, I refer to my previous post, where I comment that the static loading is, for all intents and purposes, identical to the forces encountered by a wheel bearing at rest. I also stand by my statement that the same loading on the engine bearings is presented simply by the belts themselves, and if we were to research further, it's possible we might find that the loading contributed by belts is as great as that incurred by raising the engine via the balancer. Maybe not. A lot of calculations would be required to determine that, including belt tension, the angle at which the load is applied, number of belts, etc. You have to also consider that the load exerted by jacking the engine up via the balancer is a short-term situation, whereas the load from the belts is perpetual.
Based on your explanation of your reasoning, I see your point. I concede that lifting the engine via the balancer is not the perfect way to do so, but it is an accepted practice, and in all my years working with cars, trucks and heavy equipment, particularly with diesel engines, I have never seen one damaged by doing so. On the other hand, a viscous damper, used on diesel engines, can be damaged using this method, as it has a weight inside that is surrounded by oil so that it floats and moves to the point required for balance, as that point may change due to clutch wear and numerous other factors.
Ideally, the engine should be lifted using a hoist, with attachment points on top of the engine. In the real world, that can sometimes be difficult to accomplish. I'm sure we've both seen engines supported by a jack (with a block of wood) under the oil pan. Is the oil pan designed to support the weight? Not hardly. But, in reality, design engineers know that sometimes this has to be done during repairs, so they engineer a "Factor Of Safety" into their design, and determine the shape as well as metal thickness with this in mind. Same with a crankshaft and bearings. I can say this with authority because I'm an engineer for a large supplier to all of the OEM's.
I think we've both presented our arguments clearly and concisely, and we can, as you suggested, agree to disagree at this point. Others now have facts from both of us on which to base their opinions as to which way they feel is the correct way.
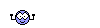