
Hobart 140 Mig butt welding help
Moderator: FORDification
- MAK
- Blue Oval Fan
- Posts: 529
- Joined: Tue Dec 21, 2004 9:35 am
- Location: Georgia, Blairsville - Florida, Flagler Beach
- Contact:
Hobart 140 Mig butt welding help
My welding sucks!
Did some more work on my floor pan today and I'm still having trouble. I was hoping someone here using the same welder could tell me what their settings usualy are for butt welding sheet metal. I think Keith had said he used the same one. The best results I can get are with it set at Voltage 2 and wire speed of about 25-30. I'm using .030 Harris "Twenty Guage". I just can't seem to get good penetration and a lot of the welds are sitting high on the top. When I crawl under the truck most of the welds aren't all the way through the seam. If I turn up the Voltage to 3 it seems too hot and I'm burning through on the 2 setting if I stay in one spot too long... Any help or suggestions would be appreciated. Thanks

- Ranchero50
- Moderator
- Posts: 5799
- Joined: Wed Nov 08, 2006 7:02 pm
- Location: Maryland, Hagerstown
- Contact:
I think the thick wire is your biggest problem Get some .023" wire and try again. The .030 is ok for structural or production work, but not sheetmetal. My baby lincoln will weld stress cracks back together on sheetmetal with .023.
Run the .023 on 1 or 2 depending on wether your welding an overlap or butting. If the weld is building up then the speed is too high. If it's hissing and puddling then the speed is too low. Usually for butt welds you need it really low and slow, hold the gun nuts steady and just hit the trigger long enough to spot the metal together, move the gun a fraction of an inch and hit it again. Walk the spots down the seam.
For me I hit it, then watch the welded spot and once the color goes away hit the next spot. If you hit it while still colorful you're more likely to melt through.
Some tips, get some goatskin gloves to weld with, they protect your hands but still allow you to feel the gun. Get an auto darkening helmet and use a drop light to keep the work area bright enough to see. It's hard to weld good when you can't see.
Jamie
Run the .023 on 1 or 2 depending on wether your welding an overlap or butting. If the weld is building up then the speed is too high. If it's hissing and puddling then the speed is too low. Usually for butt welds you need it really low and slow, hold the gun nuts steady and just hit the trigger long enough to spot the metal together, move the gun a fraction of an inch and hit it again. Walk the spots down the seam.
For me I hit it, then watch the welded spot and once the color goes away hit the next spot. If you hit it while still colorful you're more likely to melt through.
Some tips, get some goatskin gloves to weld with, they protect your hands but still allow you to feel the gun. Get an auto darkening helmet and use a drop light to keep the work area bright enough to see. It's hard to weld good when you can't see.
Jamie
'70 F-350 CS Cummins 6BT 10klb truck 64k mile Bahama Blue
Contact me for CNC Dome Lamp Bezels and Ash Tray pulls.
Contact me for CNC Dome Lamp Bezels and Ash Tray pulls.
- FoMoCo
- Preferred User
- Posts: 409
- Joined: Wed Nov 10, 2004 1:18 am
- Location: Ohio, Cincinnati
re: Hobart 140 Mig butt welding help
Get somthing copper you can put on the opposite side you are welding on. Like useing a copper backer. The copper will soak up the heat and help prevent burning though. When I welded holes in by bed side that somebody drilled, I used a piece of copper shaped like a hockey puck. I started to make a puddle in the center and puddled it out untill the hole was filled. Because the I was welding on the cooper itself it could blow though anywhere. Here's some pics. Pretend the two steel plates are you sheet metal to be but-welded. You should leave enoght space to slip a penny in between. The cooper below will absord to heat and not allow blow through. Remember, when welding, you cannot weld air.
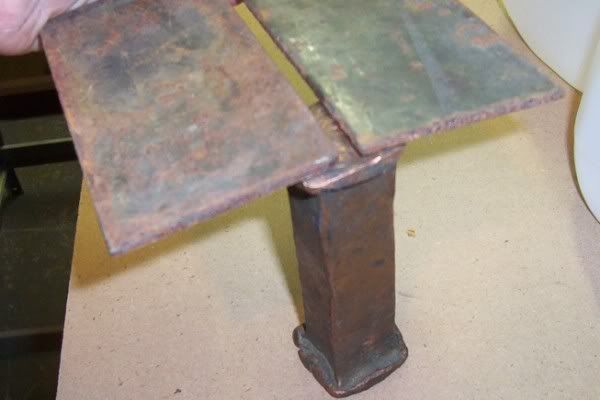
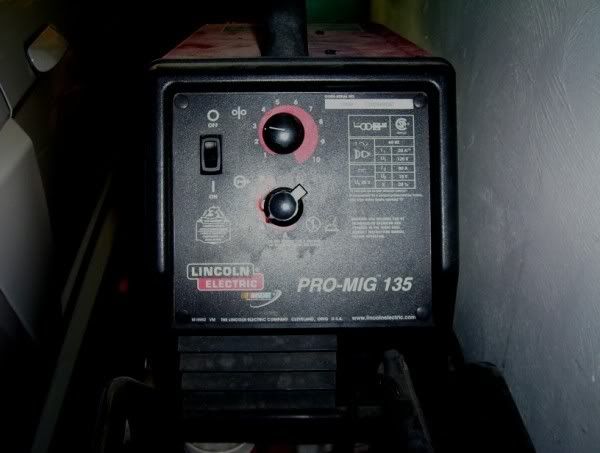
Nick
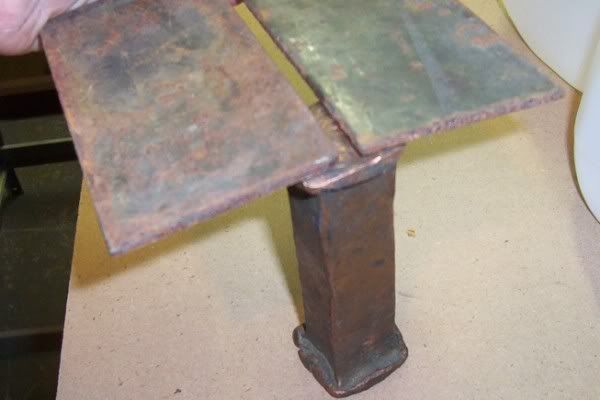
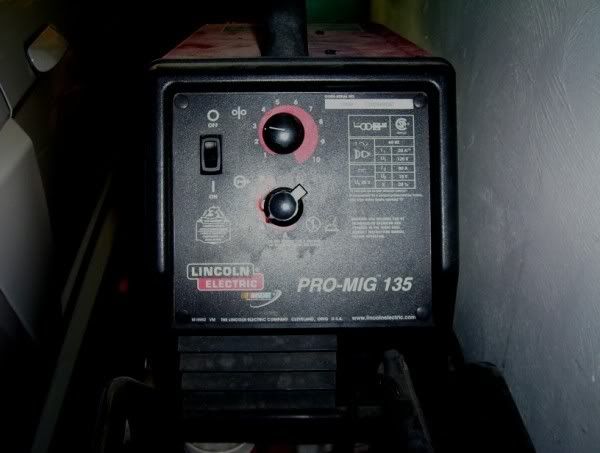
Nick
1969 F-100
2006 Fusion SEL
2006 e-320 cdi
2004 excursion V-10
2006 Fusion SEL
2006 e-320 cdi
2004 excursion V-10
- craftsman
- Preferred User
- Posts: 400
- Joined: Mon Jun 25, 2007 4:28 pm
- Location: Tennessee, Knoxville
I am having similer problems and here are some tips that i was given.
http://www.fordification.com/forum/view ... hp?t=26841
http://www.fordification.com/forum/view ... hp?t=26841
- 19674x4
- Blue Oval Fanatic
- Posts: 903
- Joined: Mon Jun 27, 2005 12:31 am
- Location: Oakland Oregon/Sheridan Wyoming
make sure you are spot welding to. just spot it enough to create a small bead of weld no bigger than say the head of a push pin by just touching the gun trigger. thengo to the other side and do the same and after you get each corner done. then go back and do the same thiing over again next tothe previous spot weld
My Photo Album
2012 Cummins-the luxury Tow Pig
1967 F-250 highboy 352, np435(((((((sold))))))))) My first true love
1968 F100 SWB. 360, np-435, flatbed, currently acting as a hornest nest and bee hive.
1971 F-100 4x4 Step-side. 360, np-435, 70k origional miles- needs allot of love.
2012 Cummins-the luxury Tow Pig
1967 F-250 highboy 352, np435(((((((sold))))))))) My first true love
1968 F100 SWB. 360, np-435, flatbed, currently acting as a hornest nest and bee hive.
1971 F-100 4x4 Step-side. 360, np-435, 70k origional miles- needs allot of love.
- Galaxie64
- New Member
- Posts: 203
- Joined: Tue Mar 21, 2006 11:51 pm
- Location: Wyoming
I second the smaller wire, it is a major PITA trying to do it with .30+ wire. I use .35 IIRC but it takes a ton of finesse and some grinding and re-welding to use it on sheetmetal. If you don't have copper a really thick chunk of steel, say 1/4" can also work. You can weld it to the sheetmetal but being as thick as 1/4" it takes a while to get it hot enough to do that and it works good for short spurts as a backer. Also using wire that big I can only spot it for the most part, trying to run a bead on sheet metal with that big of wire is all but impossible.
'68 F150 2wd
'72 F250 2wd Camper Special (400/C6/4bbl)
'64 Galaxie 500 (3524bbl/57K miles)
'92 Grand Marquis (mostly stock 4.6L)
'97 F150 (heavily modded 5.4L)
'48 F1 (Flat 6)
'51 F3 (Flat V8 )
'56 F350 (engineless)
** Chuck Norris has counted to infinity -- twice. **
'72 F250 2wd Camper Special (400/C6/4bbl)
'64 Galaxie 500 (3524bbl/57K miles)
'92 Grand Marquis (mostly stock 4.6L)
'97 F150 (heavily modded 5.4L)
'48 F1 (Flat 6)
'51 F3 (Flat V8 )
'56 F350 (engineless)
** Chuck Norris has counted to infinity -- twice. **
- MAK
- Blue Oval Fan
- Posts: 529
- Joined: Tue Dec 21, 2004 9:35 am
- Location: Georgia, Blairsville - Florida, Flagler Beach
- Contact:
re: Hobart 140 Mig butt welding help
Thanks everyone for the tips. I had tried some of the .025 wire last year when I was practicing but didn't do as well with it as I did with the Harris 20 guage. I had some recommend the Harris over regular .030 for sheet metal work and it definitely worked better for me. I'll have to spool the .025 up again and give it another try.
I had heard about using copper as a backing for filling small holes and was planning on trying that for the trim holes. Hadn't thought about using it to back the thin stuff. Will definitely give it a try for the rest of the patches.
I had heard about using copper as a backing for filling small holes and was planning on trying that for the trim holes. Hadn't thought about using it to back the thin stuff. Will definitely give it a try for the rest of the patches.